Quick Summary
Understanding the differences between ERP and MRP is essential for businesses looking to streamline their operations. While MRP systems focus on material planning and inventory management, ERP systems provide an integrated approach to managing overall business processes. Learn how these tools differ, complement each other, and help drive efficiency and growth in manufacturing and beyond.
Table Of Contents
Introduction
ERP (Enterprise Resource Planning) and MRP (Material Requirements Planning) are essential tools for optimizing business operations, but they serve different functions. ERP integrates core business processes across departments, while MRP focuses on production planning and inventory management.
Key Takeaways
Focuses on production planning, inventory management, and materials scheduling.
Integrates all business processes, including finance, HR, and supply chain management.
MRP and ERP can work together to improve efficiency and alignment.
AI, IoT, and cloud-based solutions are enhancing both systems.
Choose MRP for manufacturing-specific needs and ERP for holistic business management.
Real-time data sharing and synchronized workflows drive profitability.
MRP vs ERP: A Comprehensive Comparison
Choosing between ERP vs MRP systems—or deciding how to combine them—requires an in-depth understanding of their functions, differences, and benefits. This blog dives deep into the history, workings, and integration of these essential systems.
What is MRP?
Material Requirement Planning (MRP) is a strategic method for production planning and inventory management that ensures raw materials and components are readily available while minimizing waste and costs. It works by analyzing three key inputs: the Master Production Schedule (MPS), the Bill of Materials (BOM), and Inventory Records, By combining these inputs, MRP calculates material requirements and efficiently schedules production to meet demand.
Key Components of MRP
Demand forecasting
Inventory control
Production scheduling
Procurement management
Benefits of MRP Systems
Reduces inventory costs
Minimizes production delays
Ensures timely procurement of materials
Improves production planning accuracy
Challenges with MRP Implementation
High initial setup costs
Dependence on accurate data
Limited integration capabilities with other systems
What is ERP?
Enterprise Resource Planning (ERP) is a comprehensive software solution that integrates core business processes into a single unified system. ERP systems manage diverse functions such as finance, HR, supply chain, and customer relationships. They provide real-time data insights to improve decision-making and operational efficiency.
Core Modules of ERP Systems
Financial management
Human resources
Supply chain management
Inventory and order management
Customer relationship management (CRM)
Advantages of ERP Systems
Enhanced data accuracy and consistency
Improved cross-departmental collaboration
Scalability for business growth
Real-time reporting and analytics
Challenges of ERP Implementation
Significant time and cost investment
Complex implementation process
Requires robust change management
MRP vs ERP: Key Differences
Scope of Application
MRP systems focus exclusively on production planning and inventory control, making them ideal for manufacturing environments that require precision in material requirements and scheduling. ERP systems, on the other hand, extend beyond production to cover a wide range of business operations, including finance, human resources, customer relationship management (CRM), and supply chain management, offering an all-in-one solution.
Functionality Differences
MRP systems are specifically designed for manufacturing tasks such as material planning, production scheduling, and inventory control. They excel in ensuring raw materials are available when needed. ERP systems, however, provide a holistic solution that integrates diverse business functions, enabling seamless management of operations, from procurement and accounting to customer service and reporting.
Integration Capabilities
MRP systems can function as standalone tools or integrate with ERP systems to enhance production-specific tasks. However, ERP systems are inherently designed for integration, seamlessly connecting various departments and processes within an organization. This integration ensures real-time data sharing across functions, reducing redundancies and improving decision-making across the entire business.
When to Use MRP vs ERP
Choose an MRP system when your primary needs revolve around production efficiency, inventory control, and materials management in a manufacturing-focused operation. Opt for ERP when your business demands a comprehensive solution to manage diverse functions like finance, HR, and customer relations alongside production, ensuring streamlined operations and scalability as your business grows.
How MRP and ERP Work Together
Modern ERP systems seamlessly integrate MRP functionalities, enabling businesses to manage materials alongside other critical processes such as finance and HR. This integration allows companies to synchronize production schedules with broader business goals, aligning manufacturing workflows with financial objectives and customer demands for greater efficiency and profitability.
For instance, a manufacturing firm might use ERP-MRP software to streamline inventory management and automate procurement, while a global supply chain company leverages this combination to optimize logistics and reduce lead times, demonstrating the transformative potential of uniting these systems.
Steps to Implementing MRP and ERP Systems
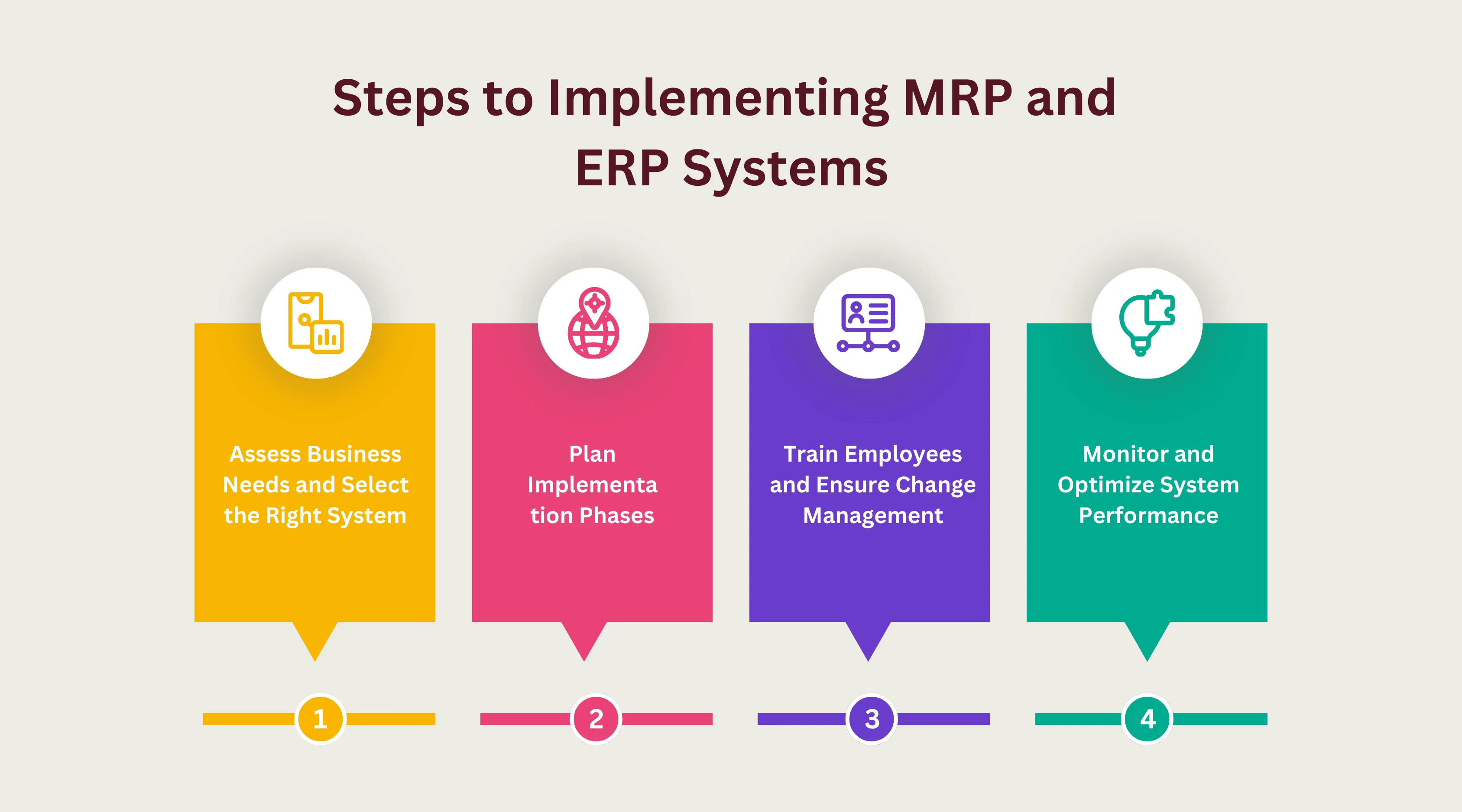
1. Assess Business Needs and Select the Right System
Evaluate your operations to determine whether you need standalone MRP or a comprehensive ERP solution.
2. Plan Implementation Phases
Divide the implementation into manageable phases, starting with critical modules.
3. Train Employees and Ensure Change Management
Provide adequate training to employees and address resistance to new systems.
4. Monitor and Optimize System Performance
Regularly evaluate system performance to identify areas for improvement.
Latest Trends in MRP and ERP Technologies
Integration of AI and machine learning for predictive analytics.
Cloud-based ERP-MRP software for enhanced accessibility and scalability.
Internet of Things (IoT) for real-time production monitoring.
Increased focus on mobile ERP solutions for on-the-go management.
Conclusion
Understanding the difference between ERP and MRP is key to optimizing your business operations. While MRP systems focus on material planning and inventory, ERP systems provide an integrated framework for overall business management. By leveraging their combined strengths, businesses can achieve greater efficiency and scalability.
Frequently Asked Questions
ERP stands for Enterprise Resource Planning. It is a software solution that integrates and manages core manufacturing operations like production, inventory, and supply chain.
Key modules include production planning, inventory management, procurement, quality control, and financial management.
The process typically includes demand forecasting, production scheduling, material procurement, quality checks, and order fulfillment.
ERP systems can be cloud-based, on-premise, or hybrid, depending on your operational requirements.
Yes, ERP software can track energy consumption, waste reduction, and compliance with environmental regulations, helping manufacturers achieve sustainability goals.
Thorough planning, employee training, and phased implementation are crucial for a smooth transition.
Yes, MRP can operate as a standalone system, especially in manufacturing-focused businesses.