Quick Summary
Manufacturing ERP systems integrate and optimize all core business processes in manufacturing industries, from production to order management and supply chain operations. By enhancing data accuracy, reducing operational costs, and improving productivity, ERP for manufacturing industries is essential for maintaining competitiveness in the market. This guide will provide a detailed understanding of ERP systems for manufacturing businesses, covering the different types, benefits, deployment methods, and key features.
Table Of Contents
Introduction
Manufacturing industries need efficient systems to manage and automate their every-day processes. Manufacturing ERP (Enterprise Resource Planning) systems offer a solution that integrates business operations like production planning, supply chain management, accounting, and more. The goal is to create a seamless workflow across the manufacturing industries.
Manufacturing ERP software helps manufacturers reduce costs, eliminate inefficiencies, and meet customer demands faster. In this guide, we will delve into what Manufacturing ERP is, explore its benefits, different system types, and deployment methods, and provide insights into how you can implement the right ERP system for your manufacturing industries.
Key Takeaways
Manufacturing ERP integrates business operations, improving productivity, data accuracy, and reducing costs.
Discrete, process, and mixed-mode manufacturing require different ERP solutions tailored to their unique production methods.
Cloud, on-premises, and hybrid ERP deployment options offer flexibility based on business needs.
Key features such as order management, supply chain management, and production planning are essential for streamlined operations.
Successful ERP implementation requires detailed planning, involving key stakeholders, and ongoing system optimization.
What is an ERP system in Manufacturing?
Manufacturing ERP is a comprehensive business management solution designed to unify and streamline operations within a manufacturing business. It consolidates processes such as inventory management, order processing, production planning, and financial accounting into one integrated system. This centralized approach allows manufacturers to make data-driven decisions, improve communication, and ensure that all departments work collaboratively toward common goals of the manufacturing industries.
Manufacturing ERP systems are typically customizable, allowing businesses to tailor them according to their specific needs. Whether a company focuses on discrete or process manufacturing, ERP systems can be adjusted to suit their unique production methodologies.
Benefits of Manufacturing ERP Software Product
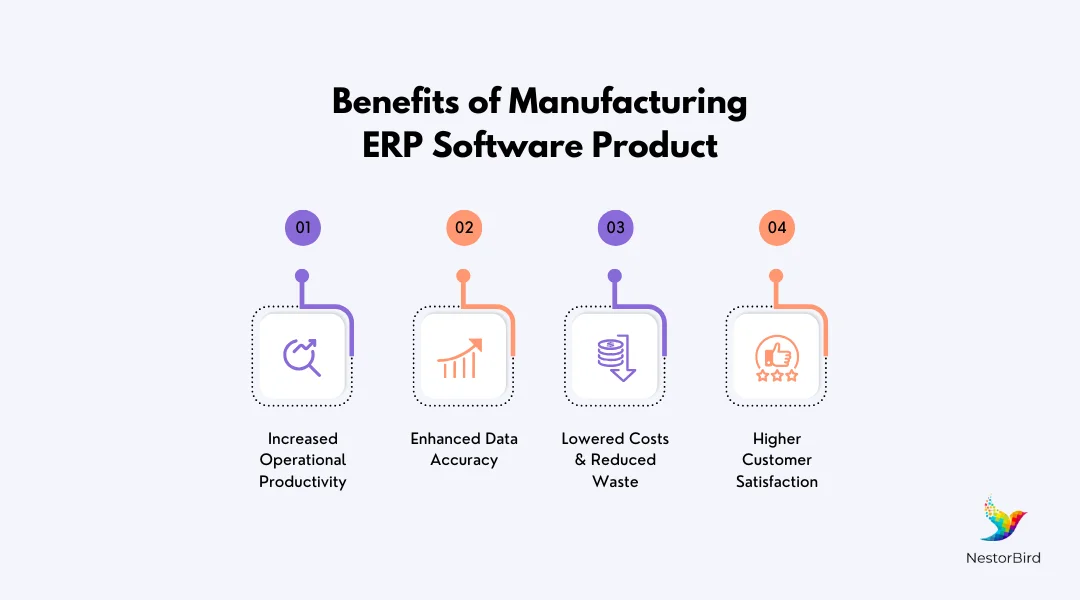
1. Increased Operational Productivity
One of the biggest advantages of implementing ERP for manufacturing is the boost in operational productivity. ERP systems automate manual processes, reducing the need for repetitive tasks and the likelihood of human error. This increased automation frees up valuable time for employees to focus on higher-value tasks, leading to faster production cycles and more efficient operations.
2. Enhanced Data Accuracy
Accurate data is the backbone of successful decision-making. Manufacturing ERP systems provide real-time data from all parts of the production and business operations. This ensures that decision-makers have access to up-to-date information, allowing them to react to changes quickly and effectively. Enhanced data accuracy also reduces the chance of costly errors, improving overall business performance.
3. Lowered Costs & Reduced Waste
By integrating business processes and increasing operational efficiency, manufacturing ERP Software Product helps reduce unnecessary costs and waste. Optimized inventory management ensures that resources are used effectively, minimizing overproduction and excess inventory. Additionally, automated workflows reduce the risk of production delays, ensuring that orders are completed on time, thereby preventing costly bottlenecks.
4. Higher Customer Satisfaction
With manufacturing ERP systems, businesses can improve the quality of their products and ensure timely delivery, two key factors in customer satisfaction. ERP systems allow manufacturers to track customer orders in real-time, ensuring that any potential issues are addressed before they become problems. The result is a smoother customer experience and a stronger reputation for reliability.
Types of Manufacturing ERP Systems
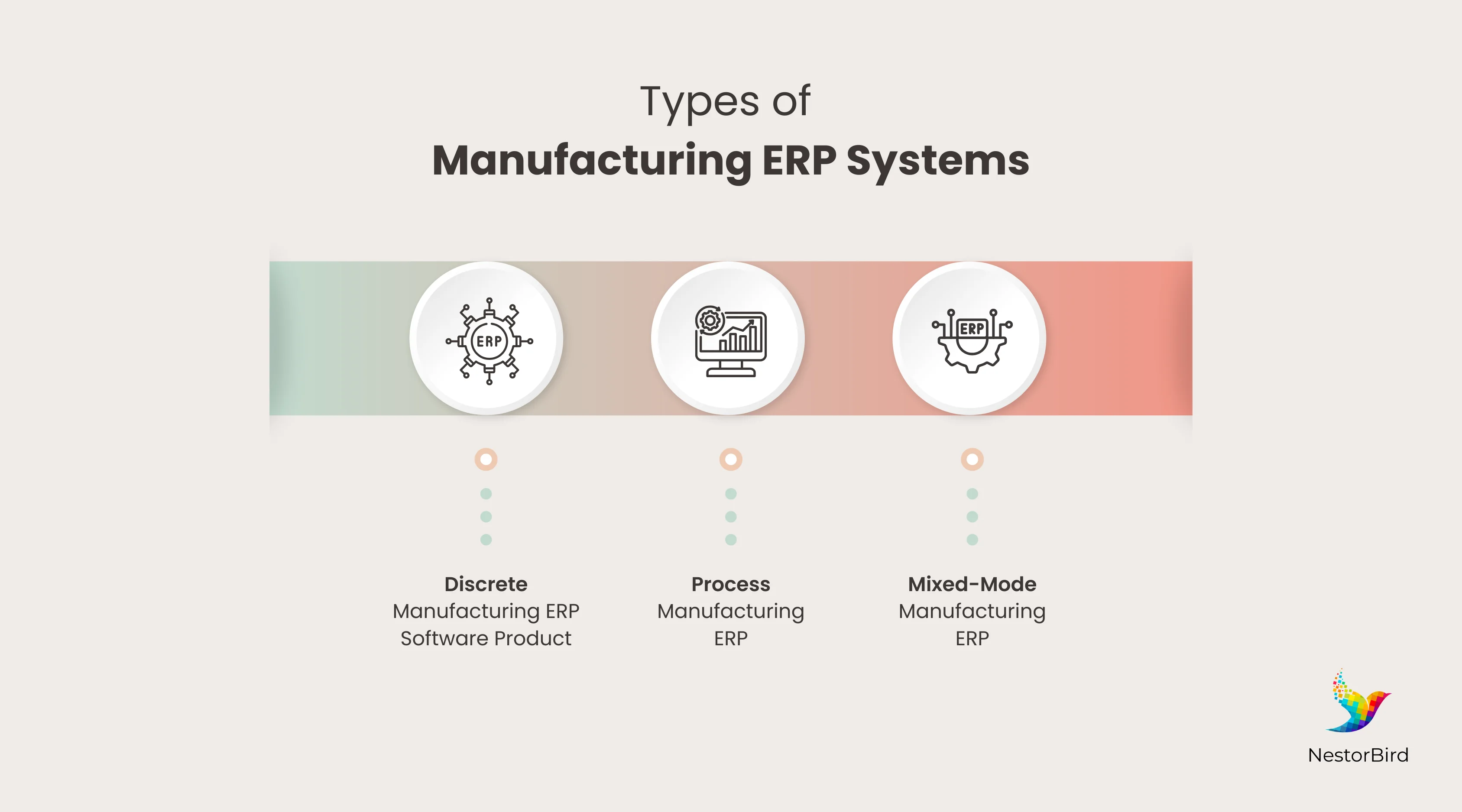
Discrete Manufacturing ERP Software Product
Discrete manufacturing involves the production of distinct items, such as automobiles, furniture, or electronics. Discrete Manufacturing ERP systems are designed to support these types of operations by providing tools for managing complex bill of materials (BOM), production scheduling, and assembly processes. These systems enable manufacturers to handle the challenges associated with producing customized or configurable products.
Process Manufacturing ERP
Process manufacturing involves the production of goods in bulk, where individual units of output are indistinguishable from each other. Industries such as food and beverage, chemicals, and pharmaceuticals rely on Process Manufacturing ERP systems. These systems manage formulas and recipes, ensuring that the manufacturing process maintains consistency and meets quality standards. Process ERP systems also help businesses adhere to regulatory requirements by tracking compliance throughout the production cycle.
Mixed-Mode Manufacturing ERP
Mixed-mode manufacturing refers to businesses that engage in both discrete and process manufacturing. These companies require ERP systems that can handle the unique challenges of both manufacturing methods. Mixed-mode Manufacturing ERP systems provide the flexibility to manage the production of distinct products while also supporting the bulk manufacturing of commodities.
ERP Deployment Methods
Choosing the right ERP deployment method is crucial to ensure that it aligns with your business needs, budget, and IT infrastructure. There are three main types of ERP deployment options:
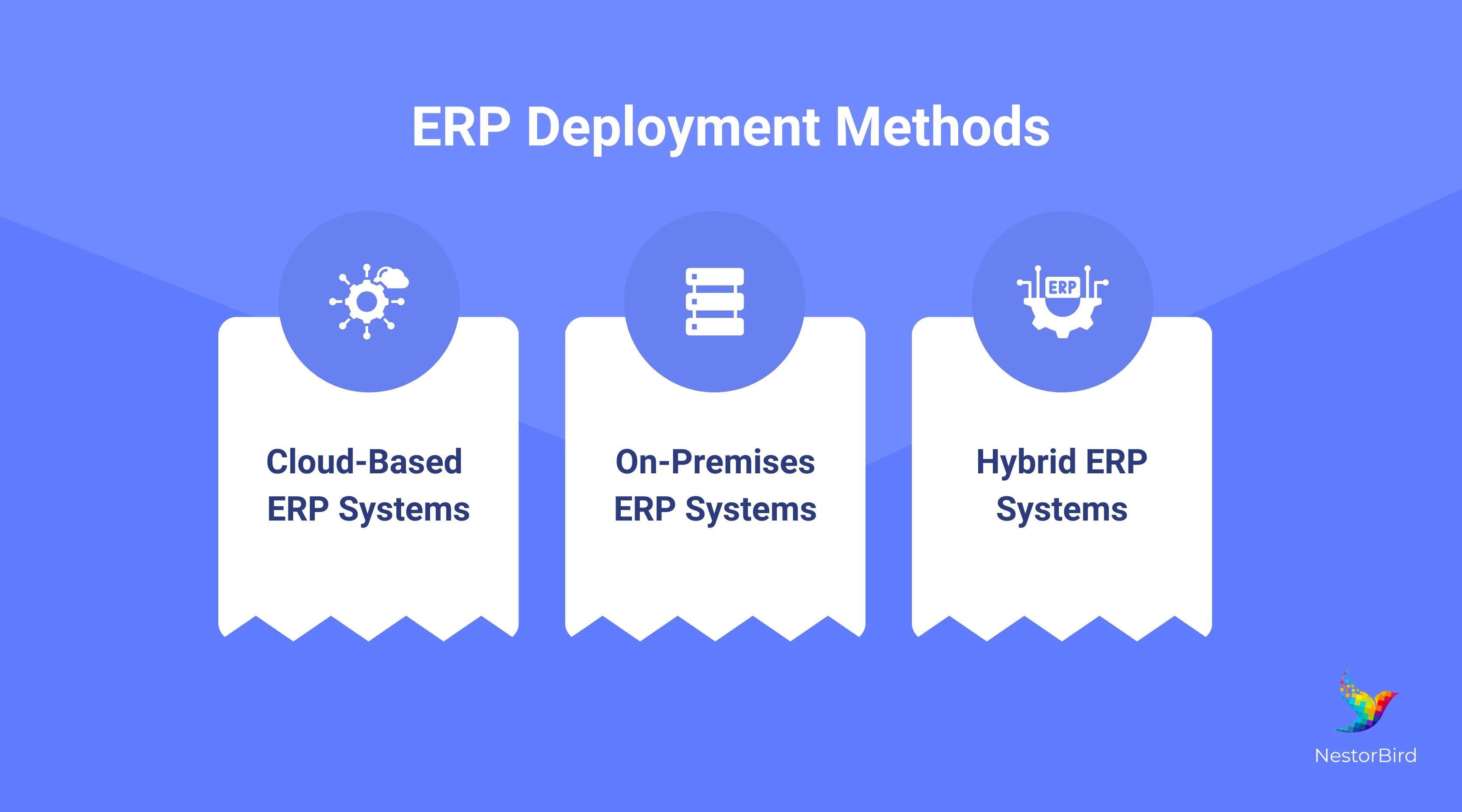
1. Cloud-Based ERP Systems
Cloud ERP systems are hosted on remote servers and accessed via the internet. One of the key benefits of cloud-based ERP is its flexibility and scalability, which makes it ideal for small-to-medium-sized manufacturing businesses. Since the system is hosted in the cloud, companies don’t need to invest in expensive IT infrastructure or maintenance. Cloud ERP systems also offer mobility, allowing users to access the system from anywhere with an internet connection.
2. On-Premises ERP Systems
On-premises ERP systems are installed and managed on the company’s own servers. This gives businesses greater control over their ERP system, particularly in terms of data security. On-premises ERP systems typically require a higher initial investment in hardware and IT personnel. However, they are favored by larger manufacturing companies that have specific data privacy and compliance needs.
3. Hybrid ERP Systems
Hybrid ERP systems combine both cloud and on-premises deployment methods, giving businesses the best of both worlds. With a hybrid approach, companies can keep sensitive data on their own servers while taking advantage of cloud-based flexibility for other functions. This allows for greater customization and control, while also offering the cost-effectiveness and scalability of cloud systems.
Key Features of Manufacturing ERP
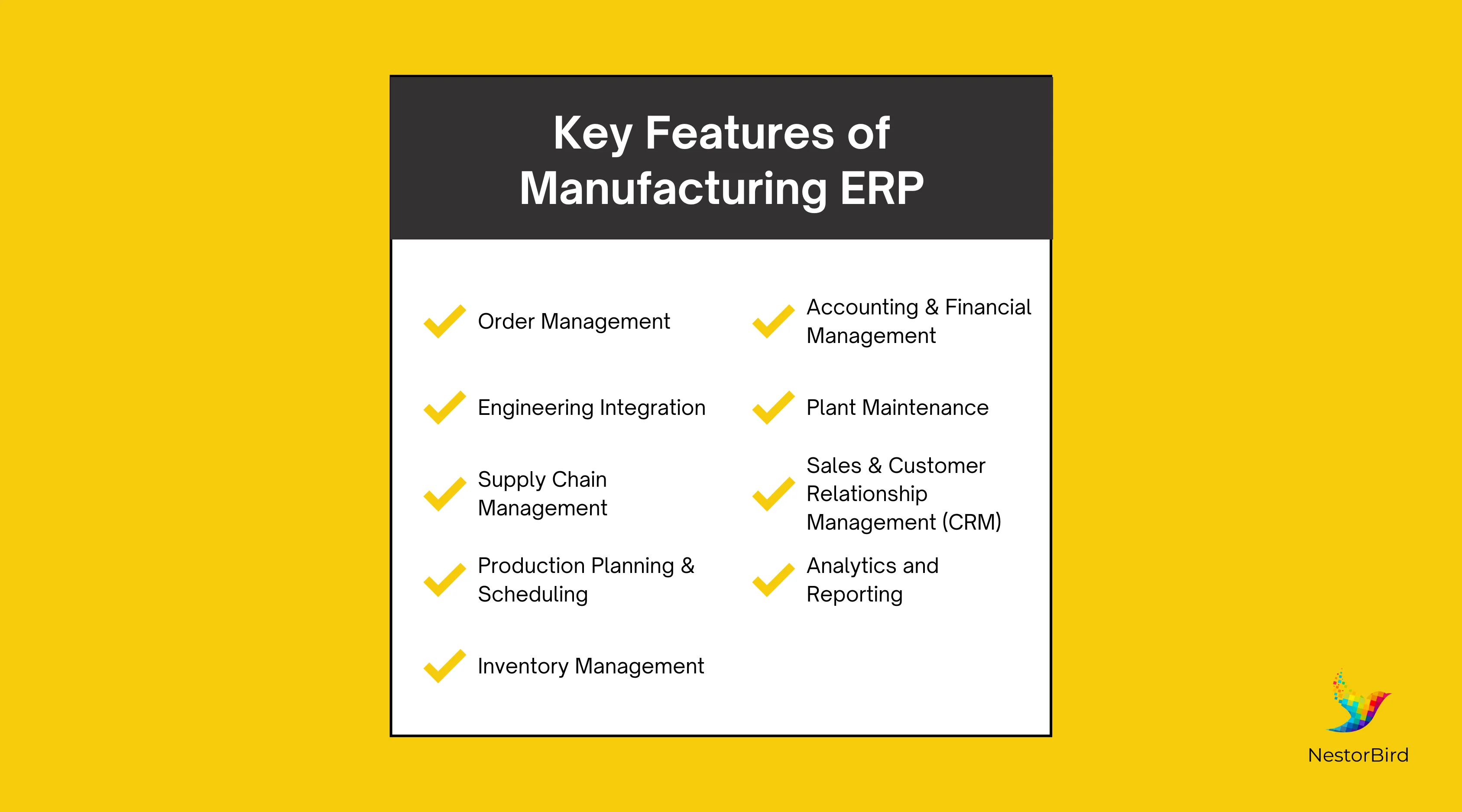
When selecting a Manufacturing ERP, it’s important to consider the key features that will bring the most value to your business. Here are some of the essential features of an ERP system for manufacturing industries:
1. Order Management
Order management functionality ensures that businesses can efficiently process and fulfill customer orders. It automates order tracking, manages order changes, and ensures timely deliveries. This feature is essential for manufacturers to improve order accuracy and customer satisfaction.
2. Engineering Integration
Manufacturing ERP systems integrate with engineering tools like CAD to ensure that product designs are correctly translated into production specifications. This minimizes errors and improves communication between engineering and production teams.
3. Supply Chain Management
An integrated supply chain management (SCM) system ensures that materials and components are available when needed, optimizing procurement and inventory levels. SCM features in manufacturing ERP also help businesses manage supplier relationships, track shipments, and streamline the entire supply chain process.
4. Production Planning & Scheduling
Production planning and scheduling tools help manufacturers optimize their production processes. These features enable businesses to plan production runs, allocate resources, and ensure that production stays on schedule. Accurate production planning minimizes downtime and maximizes resource utilization.
5. Inventory Management
Effective inventory management is critical to ensure that manufacturers always have the right amount of raw materials and components. Manufacturing ERP systems provide real-time inventory tracking, reducing the risk of stockouts and overstocking. Automated inventory management improves cash flow and reduces carrying costs.
6. Accounting & Financial Management
ERP systems include robust financial management features that allow manufacturers to manage budgets, monitor cash flow, and streamline financial reporting. Integration with other business processes ensures that financial data is always up to date and accurate.
7. Plant Maintenance
Field service management features allow manufacturers to track the maintenance and service activities of equipment used in production. This helps prevent unexpected machine failures and ensures that production runs smoothly without downtime.
8. Sales & Customer Relationship Management (CRM)
Sales CRM features enable manufacturers to manage leads, track customer interactions, and follow up on sales opportunities. By integrating CRM with manufacturing operations, businesses can ensure that customer needs are met, from the initial inquiry to post-sale support.
9. Analytics and Reporting
Manufacturing ERP systems offer powerful analytics and reporting tools that provide businesses with insights into their operations. Real-time data helps managers monitor key performance indicators (KPIs) and make data-driven decisions to optimize performance.
Which Type of Manufacturing ERP is Right for You?
Selecting the correct ERP for manufacturing businesses requires understanding your company’s size, production type, and unique requirements. Here’s a breakdown based on manufacturing types:
1. Discrete Manufacturing: These manufacturers (e.g., electronics, automotive) need ERPs that emphasize:
Customization
Order tracking
Inventory management for individual products.
2. Process Manufacturing: Ideal for industries like chemicals or food production. Look for ERPs with:
Formula and recipe management
Batch traceability
Regulatory compliance tools.
3. Hybrid Manufacturing: For businesses that combine discrete and process manufacturing, a hybrid ERP system allows flexibility in managing both types of workflows, offering tools that can handle both processes.
Key Steps to Choose:
1. Analyze Your Workflow: Evaluate key processes like production planning, order fulfillment, and resource management.
2. Identify Pain Points: Consider current challenges, such as inefficient inventory tracking or lack of regulatory compliance.
3. Set Long-Term Goals: Determine future expansion plans and scalability needs for the ERP.
4. Consult ERP Vendors: Request tailored demos and advice based on your specific industry and workflow.
Features to Consider:
Customizable ERP system: Tailor workflows, modules, and reports to suit specific business needs.
Scalability: Ensure the ERP can grow with your business.
Integration: Look for systems that integrate seamlessly with existing software, such as CRM, accounting tools, or third-party applications.
User Experience: Choose a user-friendly interface for both technical and non-technical staff.
Selecting the right ERP for manufacturing businesses is a strategic decision that should align with your operational goals, production type, and business growth plans. Carefully assess vendors and solutions to ensure you find a system that enhances productivity, compliance, and long-term success.
How to Successfully Implement Manufacturing ERP
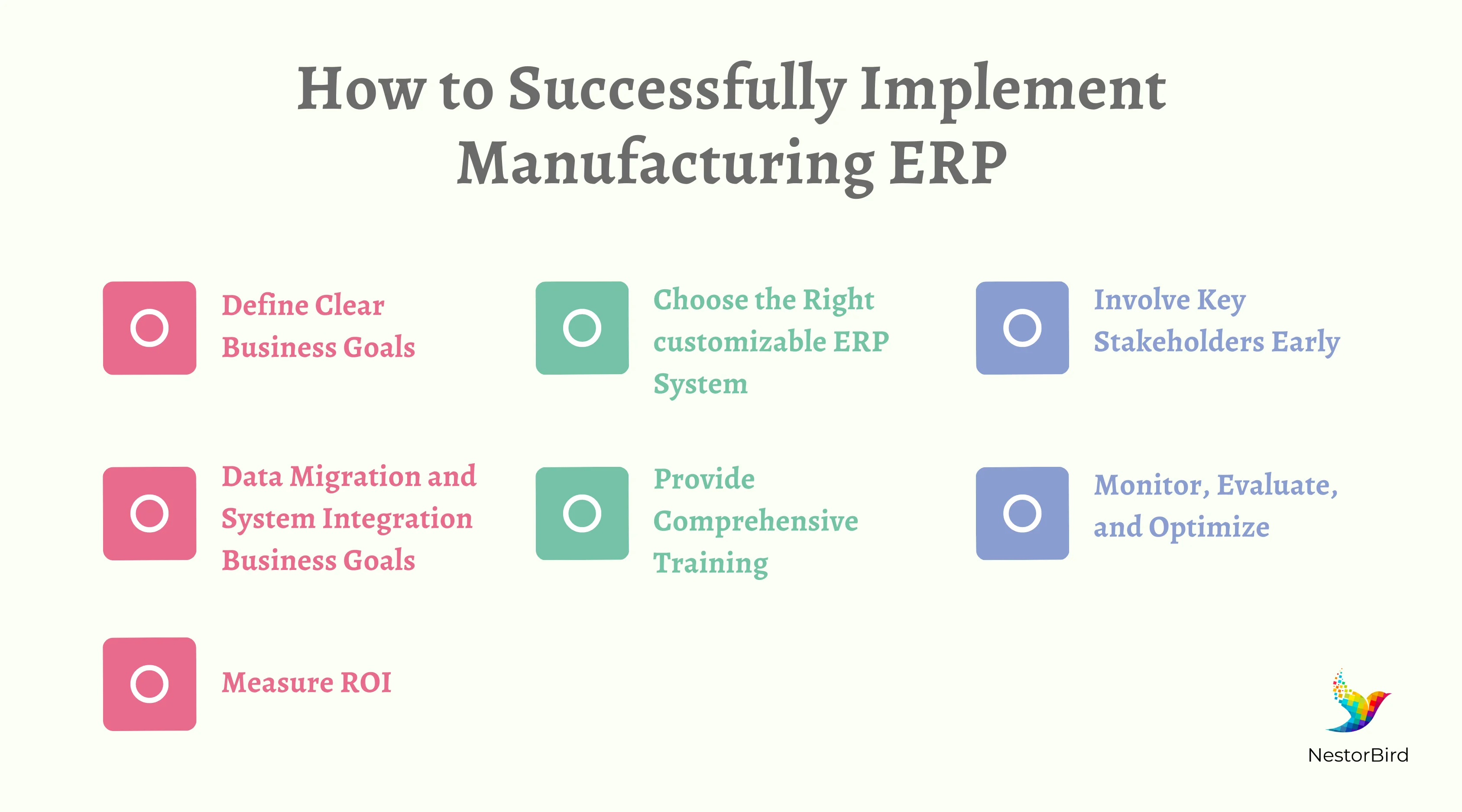
1. Define Clear Business Goals
Set specific objectives such as improving production, reducing costs, or enhancing inventory management. These goals will drive the ERP’s configuration and usage.
When explaining technical concepts like ERP implementation, always tie objectives to real-world outcomes. Use clear, concise language and break down jargon so your audience—especially non-experts—can grasp the importance of each goal. If you’re struggling to simplify or polish your wording, consider using a sentence rewriter tool to refine your phrasing while keeping the original meaning intact.
2. Choose the Right customizable ERP System
Select an ERP tailored to manufacturing needs (discrete or process manufacturing). Consider deployment options like cloud, on-premises, or hybrid systems, based on your company’s size, infrastructure, and scalability needs. Cloud solutions are cost-effective, while on-premises offer more control but at higher costs. Hybrid systems can provide flexibility.
ERP Features to Consider:
Production Planning and Scheduling: Optimize workflows, manage resources, and improve efficiency.
Inventory Management: Ensure accurate stock tracking and reduce waste.
Supply Chain Management (SCM): Strengthen relationships with suppliers, improve lead times, and handle logistics.
Quality Management: Implement measures to control product quality at every stage.
Financial Management: Integrate costing, budgeting, and financial reporting.
3. Involve Key Stakeholders Early
Engage department heads (production, procurement, IT, finance) in the selection and planning process. Their involvement ensures the system addresses real operational needs, increases buy-in, and eases resistance to change.
Project Teams: Establish a cross-functional implementation team that includes technical staff, process owners, and executive sponsors to ensure different perspectives are represented.
4. Data Migration and System Integration
Plan and carefully execute data migration from legacy systems. Data cleansing is essential to avoid transferring outdated, incorrect, or redundant information into the new ERP.
Ensure seamless integration with existing software tools (e.g., CRM, CAD software, or IoT platforms) for a holistic view of operations.
5. Provide Comprehensive Training
Invest in extensive training for all users, from factory floor workers to management. Different levels of training (basic to advanced) should be tailored to specific roles, ensuring that employees are proficient with the system.
Implement a change management strategy to address employee concerns and ensure smooth adoption.
6. Monitor, Evaluate, and Optimize
Post-implementation, closely monitor the system to ensure it meets the expected goals (e.g., increased efficiency, improved production timelines).
Conduct periodic reviews to identify bottlenecks or areas for improvement, and adjust processes as needed.
Continuous Improvement: ERP is a long-term investment; continuously optimize its functions by updating modules, incorporating feedback, and staying current with industry trends.
7. Measure ROI
Track the ERP’s performance in areas like cost savings, lead time reduction, and enhanced productivity. This will help in justifying the investment and fine-tuning system configurations.
By following these steps and investing in the right ERP solution for your manufacturing environment, you can expect improved operations, better decision-making, and greater agility in responding to market demands.
Frequently Asked Questions
Manufacturing ERP is a comprehensive system that integrates all business processes within a manufacturing company, including production, inventory, and finance.
Manufacturing ERP systems improve efficiency by automating manual tasks, enhancing data accuracy, and optimizing resource allocation, leading to faster production cycles and lower operational costs.
Key features to look for include supply chain management, production planning, inventory management, order tracking, and real-time analytics.
Consider your production methods (discrete, process, or mixed-mode), deployment options (cloud, on-premises, or hybrid), and the specific features that will best support your business operations.
Common challenges include resistance to change, lack of user training, and inadequate planning. Clear communication and training are essential to overcoming these challenges.
Future trends in manufacturing ERP include AI-driven analytics, IoT integration for real-time data collection, and increased cloud adoption for scalability and cost efficiency.
The implementation timeline can vary from several months to over a year, depending on the complexity of the system and the size of the company. Planning and training are critical factors in ensuring a smooth rollout.