Quick Summary
Manufacturing ERP systems are designed specifically for the manufacturing sector, providing tools like production planning, inventory management, and quality control. Traditional ERP, on the other hand, is a versatile, general-purpose solution that caters to a broad range of industries but lacks manufacturing-specific functionalities.
Table Of Contents
Introduction
How do you decide between manufacturing ERP and traditional ERP? While traditional ERP systems are built for general business processes, manufacturing ERP systems cater specifically to production-heavy industries, offering advanced tools for shop floor management and real-time insights. Understanding their differences and applications is critical for making an informed decision. In this article, we’ll compare manufacturing ERP and traditional ERP, outline their features, and guide in choosing the best solution for your business needs.
Key Takeaways
Manufacturing ERP offers specialized tools for production, unlike traditional ERP.
Manufacturing ERP provides shop floor visibility, aiding decision-making.
Manufacturing ERP systems are better suited for growing production needs.
Traditional ERP is more affordable but lacks industry-specific modules.
Choose manufacturing ERP for production-centric businesses and traditional ERP for general industries.
Understanding ERP
What Is a Traditional ERP System?
A traditional ERP (Enterprise Resource Planning) system is a centralized platform designed to manage essential business operations such as accounting, human resources, procurement, and supply chain management. It streamlines workflows, improves efficiency, and enables data sharing across departments.
What Is a Manufacturing ERP System?
A manufacturing ERP system is a specialized solution tailored to the unique needs of manufacturing businesses. It integrates core business processes with industry-specific functionalities like production planning, inventory management, shop floor control, and quality assurance. These systems are designed to optimize workflows, reduce waste, and ensure real-time visibility into manufacturing operations.
Key Differences Between Manufacturing ERP and Traditional ERP
When considering operational tools for your business, it's crucial to understand the distinctions between traditional management software and Enterprise Resource Planning (ERP) systems. While traditional tools often address specific tasks, ERP systems provide a comprehensive, unified solution designed to streamline and optimize business processes across departments.
Traditional Management Software
Traditional software solutions are typically designed to handle isolated functions. For example, a small business might use one software for accounting, another for inventory management, and a separate CRM (Customer Relationship Management) tool for customer interactions. While effective in their domains, these tools often operate in silos, leading to:
Data Fragmentation: Data is scattered across multiple systems, making it difficult to access a unified view of operations.
Manual Integration Challenges: Connecting different systems often requires manual updates or third-party integrations, increasing the risk of errors.
Limited Scalability: Adding new features or integrating additional processes becomes cumbersome as the business grows.
Modern ERP Systems
ERP systems, on the other hand, are designed to provide an end-to-end solution by integrating core business functions into a single, cohesive platform. Instead of juggling multiple tools, an ERP allows businesses to manage operations seamlessly with shared data and real-time visibility. Key features include:
Centralized Data: ERP systems ensure that all departments—finance, sales, HR, inventory, and customer service—operate from a single source of truth.
Process Automation: Tasks such as order processing, payroll, and inventory updates are automated, reducing errors and improving efficiency.
Advanced Analytics: ERPs provide real-time dashboards and reporting tools, enabling data-driven decision-making.
Scalability and Flexibility: A customizable ERP system grows alongside your business, allowing you to add features or expand into new markets without overhauling your processes.
When to Choose Manufacturing ERP
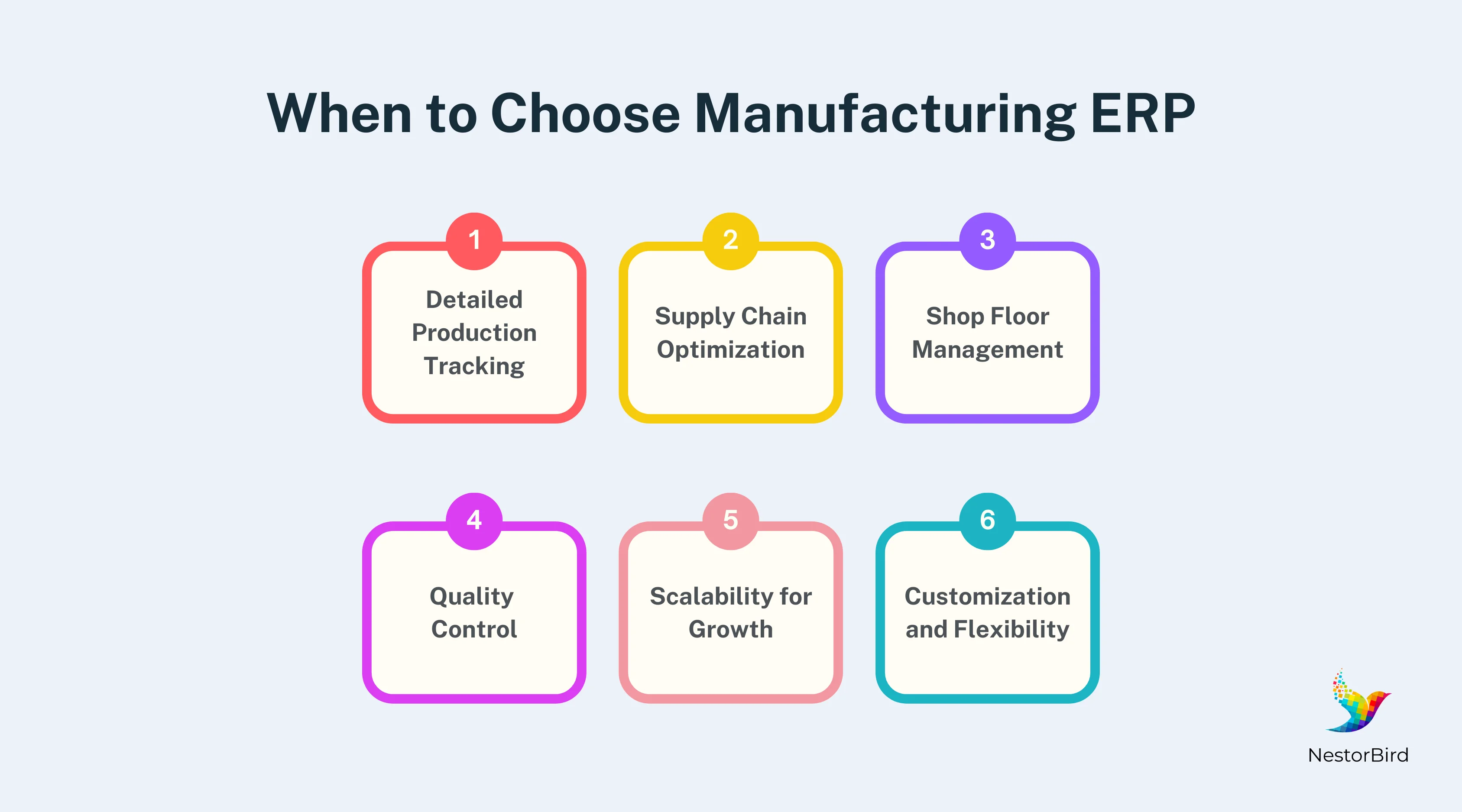
Manufacturing ERP systems are ideal for businesses with complex production processes and a need for industry-specific tools. Opt for a manufacturing ERP if your organization requires:
Detailed Production Tracking: Manufacturing ERP provides real-time insights into production schedules, machine utilization, and order progress, helping to improve efficiency and reduce downtime.
Supply Chain Optimization: These systems streamline procurement, inventory management, and logistics, ensuring smooth coordination between suppliers, warehouses, and production lines.
Shop Floor Management: Manufacturing ERP integrates with shop floor equipment, offering features like machine monitoring, workforce management, and production line optimization.
Quality Control: With modules focused on quality assurance and compliance, a manufacturing ERP helps maintain product standards and reduces defect rates.
Scalability for Growth: If your business plans to expand, manufacturing ERP systems can scale to support increased production capacity and new operations.
Customization and Flexibility: Designed to meet the unique demands of the manufacturing sector, these systems offer customizable modules that align with specific production requirements.
When to Choose Traditional ERP
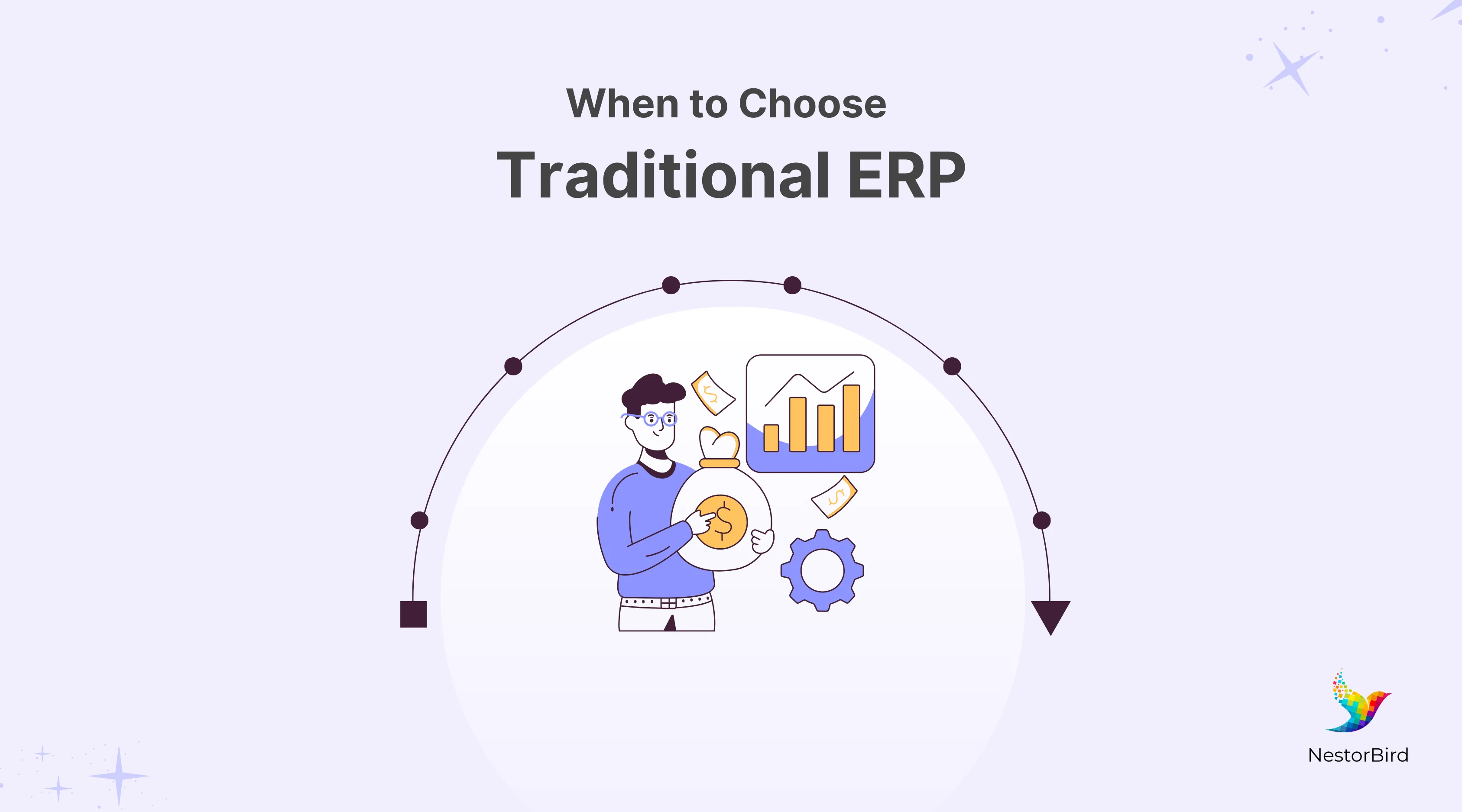
Traditional ERP is an excellent choice for businesses that require a comprehensive, general-purpose system to manage core processes like accounting, human resources, customer relationship management (CRM), and supply chain operations. It is particularly suitable for industries such as retail, healthcare, and services where production-specific functionalities are not a priority.
Additionally, traditional ERP systems are often more cost-effective, making them a practical option for small to medium-sized enterprises (SMEs) or organizations with budget constraints. These systems provide robust integration across departments and ensure smooth information flow, improving overall efficiency without the added complexity of manufacturing-specific tools.
Choose traditional ERP when:
Your operations do not include complex manufacturing processes.
You prioritize managing financials, HR, and logistics over production workflows.
Your business seeks scalability but can use something other than shop floor control or production planning features.
You need a cost-effective solution with the flexibility to customize for diverse industry use cases.
Key Factors to Consider Before Implementing ERP

1. Assessing Business Needs
Identify pain points and inefficiencies in your processes. Focus on areas like inventory management, HR, sales, or production. Determine whether you need general functionalities or industry-specific features to address these challenges effectively.
2. Choosing the Right Deployment Type
Decide between cloud-based, on-premises, or hybrid ERP systems. Cloud solutions offer flexibility and lower upfront costs, while on-premises systems provide greater control and long-term savings. Hybrid options combine the benefits of both.
3. Cost and Budget Planning
Understand the total cost of ownership (TCO), including licensing, implementation, maintenance, and training. Compare the costs of cloud-based subscriptions versus on-premises investments to ensure alignment with your budget.
4. Scalability and Integration
Choose an ERP system that can grow with your business. It should integrate seamlessly with existing tools like CRM, accounting, and supply chain software to maintain operational efficiency as your business expands.
5. Ease of Use and Training
A user-friendly interface and robust training resources are essential for successful adoption. Opt for an ERP solution that minimizes the learning curve and provides ongoing support for your team.
6. Vendor Reliability and Support
Vendor Reliability and Support Research vendors’ track records, customer reviews, and industry expertise. Choose a vendor that offers strong customer support, regular updates, and customization options to ensure your ERP system meets your evolving needs.
Conclusion
The choice between manufacturing ERP and traditional ERP depends on your business goals and requirements. Manufacturing ERP software is ideal for production-centric industries, while traditional ERP serves broader business needs. By choosing the best ERP software tailored to your needs, you can unlock unprecedented efficiency and scalability. Whether you’re a small business owner or managing a medium enterprise, an ERP system is your gateway to streamlined success.
Frequently Asked Questions
ERP systems integrate business functions, while traditional systems are siloed and lack cross-departmental capabilities.
Common ERP systems for manufacturing include SAP S/4HANA, Oracle NetSuite, and Microsoft Dynamics 365.
Traditional ERP suits industries like retail, healthcare, and finance that don't require specialized manufacturing tools.
Manufacturing ERP is ideal for industries like automotive, aerospace, and consumer goods, requiring production-focused functionalities.
Consider your industry, specific needs, and budget. Manufacturing ERP is best for production-heavy industries, while traditional ERP suits diverse businesses.